1,3-BAC Features
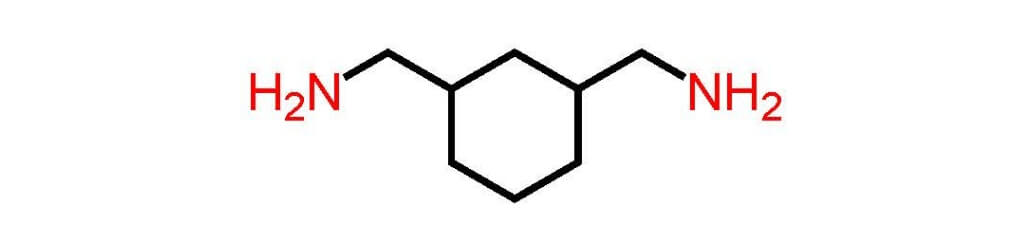
✔Low viscosity (9.1 mPa・s @ 25°C) ✔High Tg (>125°C) ✔Fast curing (120°C gelling 1 minute)
1,3-BAC’s characteristics as an epoxy curing agent are low viscosity, fast curing, and high Tg. These characteristics make it suitable as a curing agent for RTM molding such as FRP applications. 120°C curing in 3 to 5 minutes is possible, and the Tg after molding is over 125°C, providing high heat resistance.
HP-RTM molding with 1,3-BAC
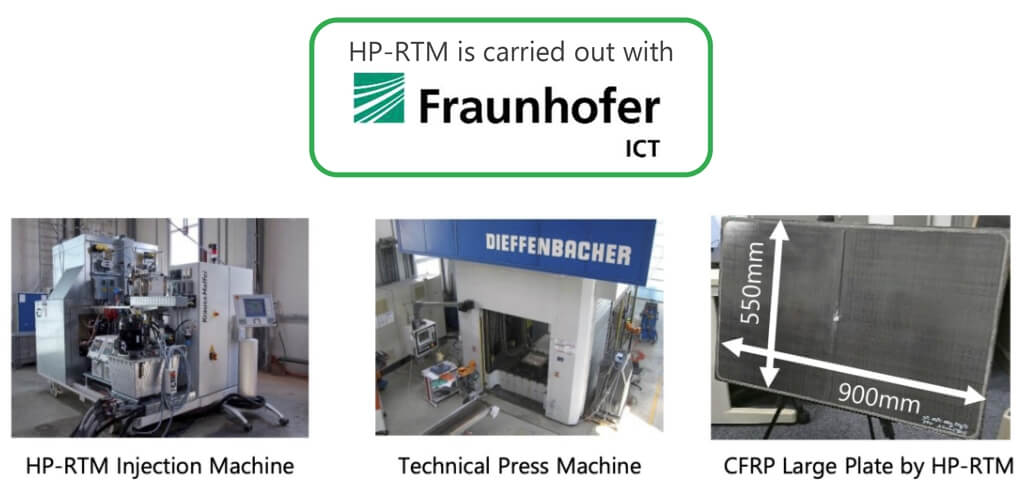
We have conducted moldability verification using actual HP-RTM molding equipment and confirmed that molding of large CFRP with high flowability is possible.
Examples of HP-RTM molding conditions
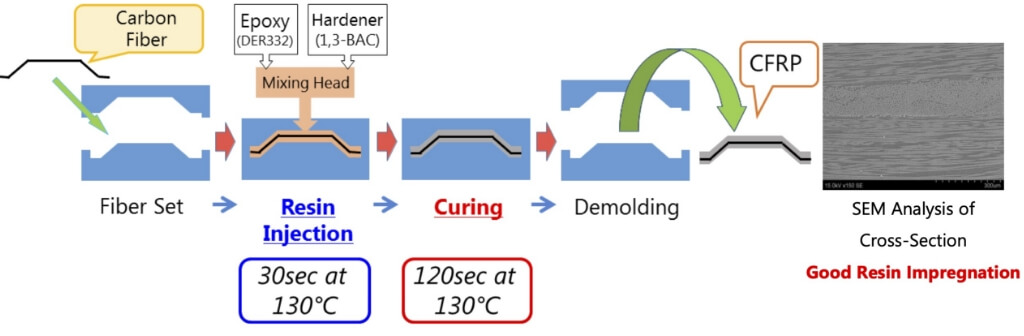
Large-size parts can be produced with long pouring time and mass production with high-cycle molding.
HP-RTM is a molding method to produce FRP by injecting a mixture of epoxy and curing agent into a heated mold in which a fiber base material is set, and curing the mixture in the mold. This enables high-cycle (short-time) molding, which is required in the molding of automotive parts.
Recommendation
Example of Epoxy Resin formulation
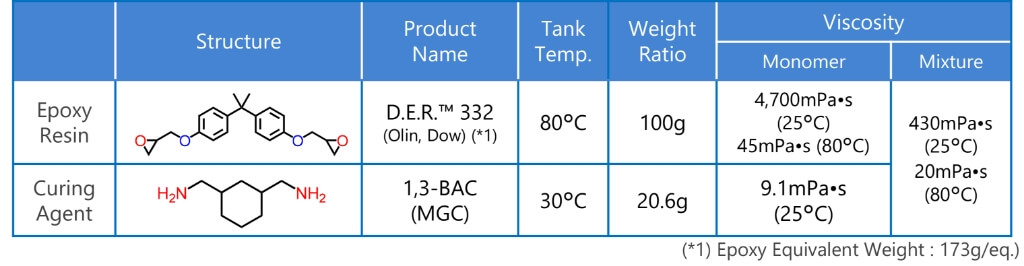
Comparison of resin viscosity per curing agent (at 80°C)
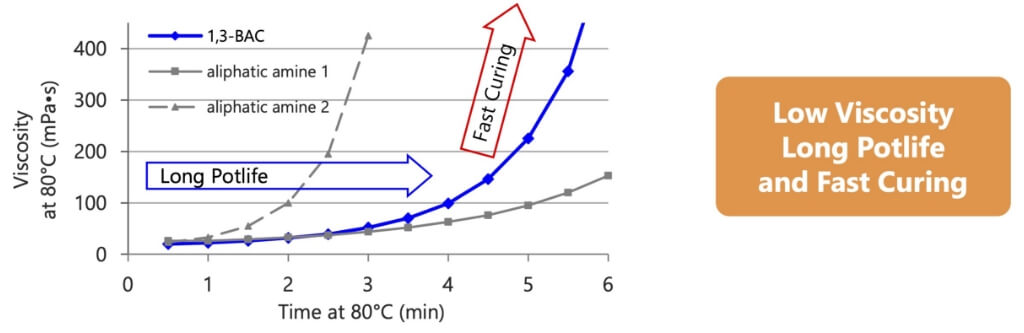
Cured resin Tg
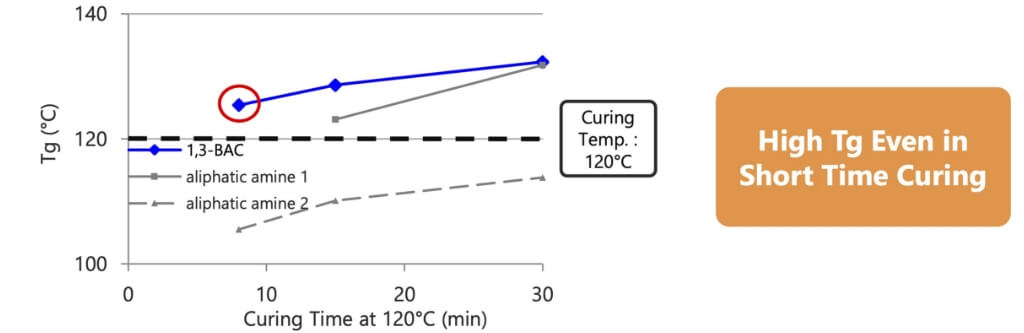
CFRP Physical Properties
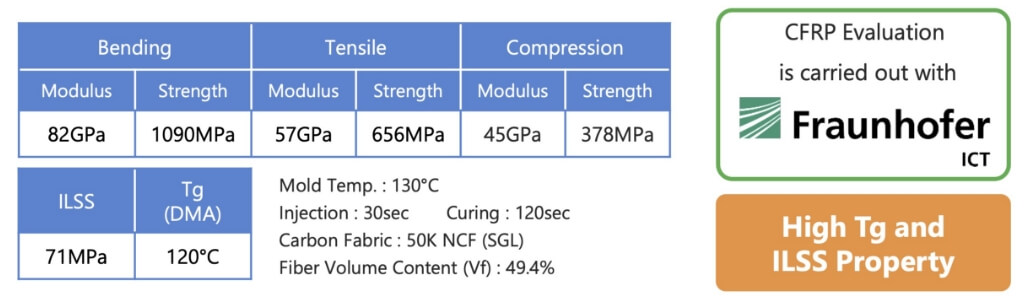
As a recommended formulation, a ratio of 22 g of 1,3-BAC to 100 g of general-purpose BisA epoxy can be used. 1,3-BAC is fast curing, yet retains a low viscosity state for a long time, which allows it to flow in the mold, which is its most important feature for RTM molding. Furthermore, the resulting CFRP has high Tg and high ILSS properties.
Formulating Additives
Example of accelerator addition
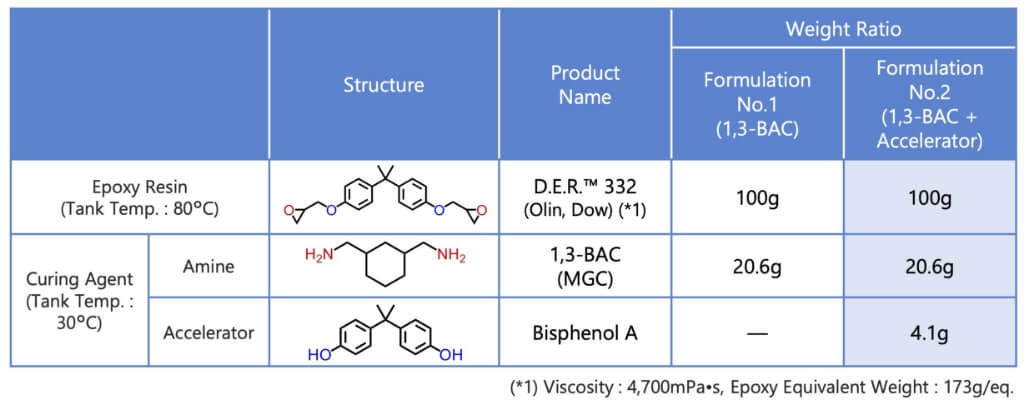
HP-RTM process temperature and time
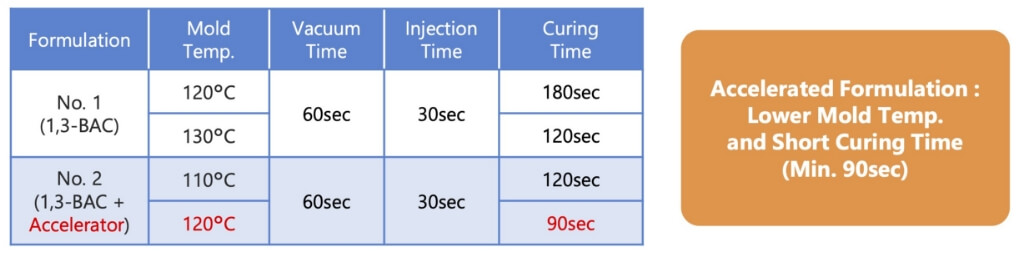
The curing agent can be formulated not only as 1,3-BAC alone, but also with additives such as accelerators to adjust the curing speed. The formulation can be made to cure quickly at low temperatures, thus reducing energy consumption during the molding process.
1,3-BAC Physical Properties
1,3-BAC Physical Properties

Carbon Fiber Properties Used in HP-RTM

HP-RTM conditions

Detailed values of 1,3-BAC physical properties, carbon fibers used in HP-RTM molding, and equipment conditions are shown.
1,3-BAC and hydrogenated BisA epoxy
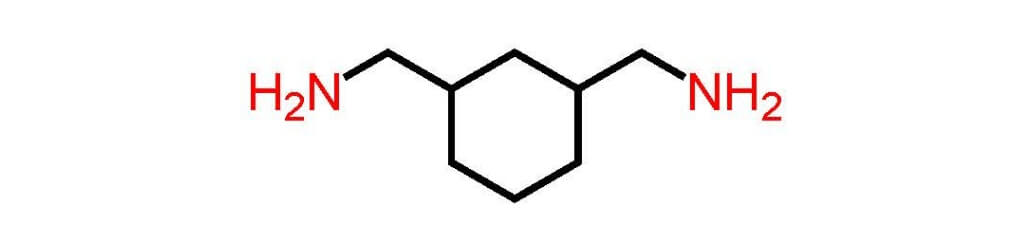
✔Resistant to yellowing under UV environment ✔High reactivity and fast curing
For molding two-component epoxy resins
Yellowing due to UV is an issue for CFRP automotive exterior parts that are directly exposed to sunlight. By combining hydrogenated BisA epoxy and 1,3-BAC, formulations for RTM molding with particularly excellent resistance to yellowing can be obtained.
UV resistance test (ISO 4982)
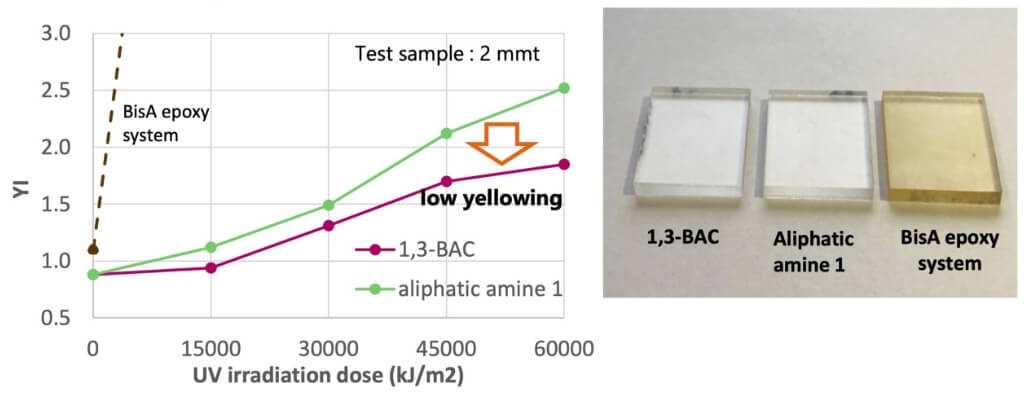
In UV irradiation tests using Xe lamps (300-400 nm) in accordance with ISO 4982, 1,3-BAC’s excellent resistance to yellowing is confirmed.
HP-RTM Molding
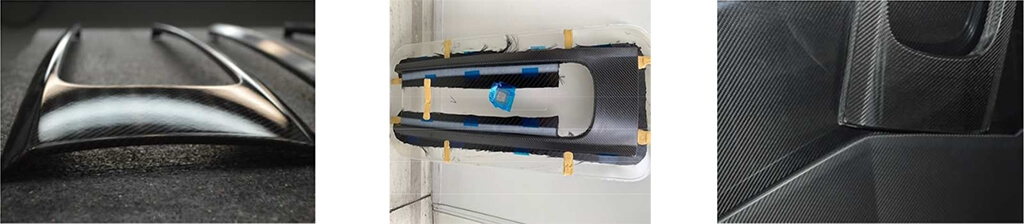
Existing RTM molding materials are made of resin that tends to yellow, requiring several coats of acrylic paint to be applied to the molded product to prevent yellowing. On the other hand, the 1,3-BAC formulation using hydrogenated BisA epoxy can be processed by simply polishing the surface, offering advantages in terms of cost and productivity.
Reaction rate proportional comparison (at 105°C)
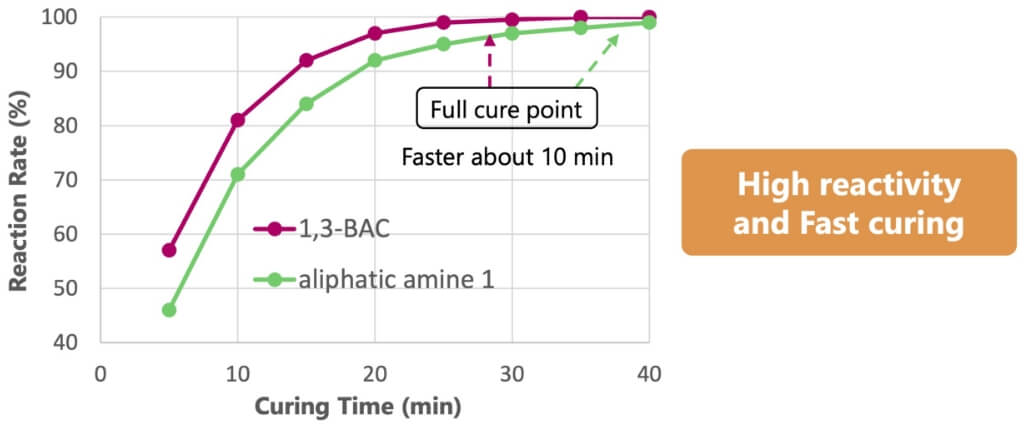
Hydrogenated BisA epoxy has a slower reaction rate than general-purpose BisA epoxy, but 1,3-BAC is also characterized by its fast curing properties, allowing the reaction to be completed at 105°C/30 minutes.
Process conditions at HP-RTM
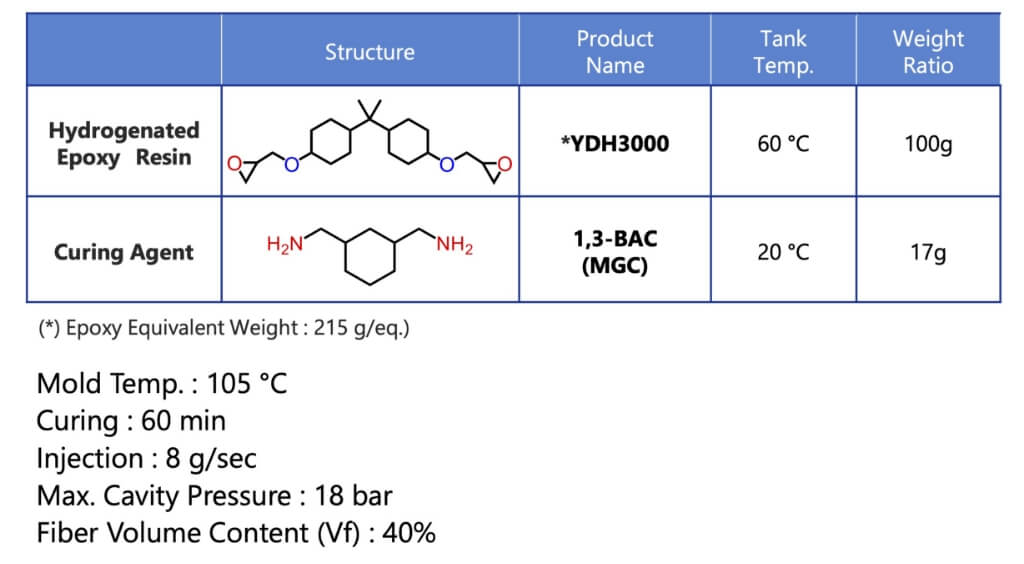
Typical hydrogenated BisA epoxy and 1,3-BAC blends are shown.
※YDH3000:Made by Aditya Birla EPOTEC ®